What İs a Check Weigher ?
What Should Be Considered
A belt check weigher is a system that weighs products in motion as they pass over a load cell on a production line. The belt checkweigher now has features far beyond weighing and offers many advantages for users. It also looks at the various dynamic load cell technologies that can be used and their suitability for different types of applications and production environments.
When it comes to checkweighing, there is no single “one size fits all” solution, but it is important for both manufacturers and end-users to better understand why the load cell selection process should be based on the level of accuracy for the application in question, as well as the ambient conditions and product handling parameters, so that they can select the ideal load cell for their own operational needs.
In checkweigher systems, products are grouped into predefined weight zones and then sorted or removed according to the weighing classification. The belt checkweigher collects and processes data continuously in a fraction of a second to ensure high accuracy. This process is important for checkweigher systems to provide efficient results.
We can list the main issues to be considered in the selection of belt control systems as follows
1.Definition Of The Control System Needed
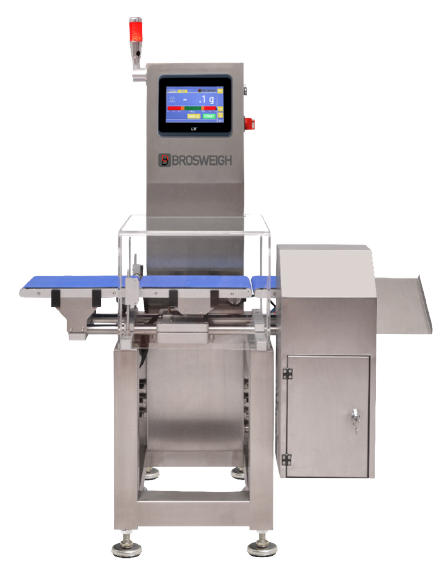
The first factor to consider when selecting a system is the functionality required.
- Whether there will be detection of metal particles as well as dynamic weighing control
- Whether there will be product labeling after inspection
- Whether non-conforming products will be sorted manually or automatically
- Whether it is desirable to sort or classify packages according to measured weight
- The answer to these questions will be the starting point for creating the ideal system
2. Product Description
The right machine project should be based on the evaluation of shape, dimensions, weight range, packaging and all other product defining elements.
-Shape
Products with thin bases, too long for the footprint and rounded shapes are all unstable and require some special design to prevent them from falling as the conveyor passes over the line. On the contrary, product groups with large bases and non-rounded shapes are subject to less vibration and will not be a critical point.
– Packaging
The weighing accuracy required for a bottled liquid product differs greatly from that required for counting the components of a box. The question of whether the products to be checked will be packaged or bulk is also of great importance.
– Loose Products
Packages containing granular and powdery products tend to lose some particles during transportation, with the risk of altering the scale result. This should be taken into account by the manufacturer as appropriate, such as providing open-work conveyors to prevent the accumulation of debris.
– Liquid or Viscous Products
Liquid, viscous or very slightly compact products are subject to internal movements due to vibrations caused by movements on conveyors. The greater the friction and viscosity, the greater the weighing variations as it is difficult for the product to move from one conveyor to another. For this reason, the design phase of the conveyor line should be considered in the best way.
– Weight and Speed
Product weights and the amount of product to pass through are of great importance in the selection of chekweigher systems. The determination of the range of product weight to be passed, the number of products per minute requested, whether the products are requested to be passed in grams or kilos, are the main issues to be determined. The higher the speed of the conveyors, the lower the maximum possible accuracy. Likewise, the products must have the correct ranges to avoid multiple products passing through the weighing scale at the same time and forging the result.
– Metal Risk
Products have the risk of exposure to metal particles during manufacturing. It is necessary to determine whether the appropriate law requires metal detection. “Metal Detector” should be used in the systems for metal risk, which is one of the issues to be considered especially in the food and chemical sectors. Determining the appropriate metal detector is of great importance. The metal detector detects ferrous, non-ferrous and other foreign metal substances of the smallest size using digital signal processing technology.
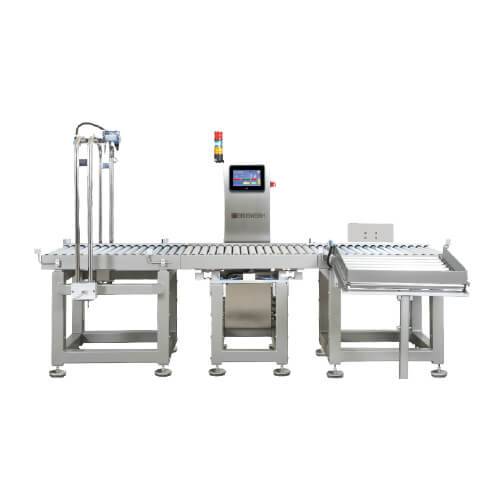
3. Working Environment
The environment in which the belt check weigher system will operate directly affects the system. This effect should be evaluated well.
- Temperature: The temperature of the working environment directly affects the system. Repeated and significant fluctuations in temperature can change the weighing results.
- Humidity and Washing: It should be determined whether washing is done in the environment where the belt checkweigher system is desired to be installed, and if so, what kind of washing method is used.
- Debris and Dust: It should be determined whether there are volatile particles and dust particles in the environment where the belt checkweigher system is desired to be installed and whether the machine will be exposed to dust accumulation.
- Vibration : In the environment where the belt check weigher system is desired to be installed, it should be determined whether the ground on which the machine will stand is exposed to vibration and air currents.
- Corrosion : In the environment where the belt check weigher system is to be installed, it should be determined whether the machine will be exposed to corrosion risk. The first and most important factor to be evaluated will be the degree of insulation of the check weigher system.
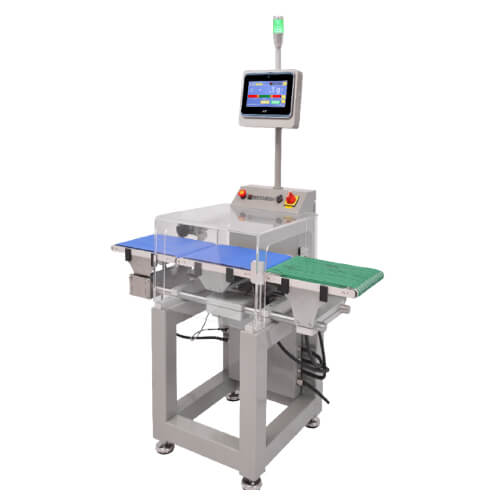
You can check this link to review and order BrosWeigh Check Weigher. You can click on this lnk for similar resources